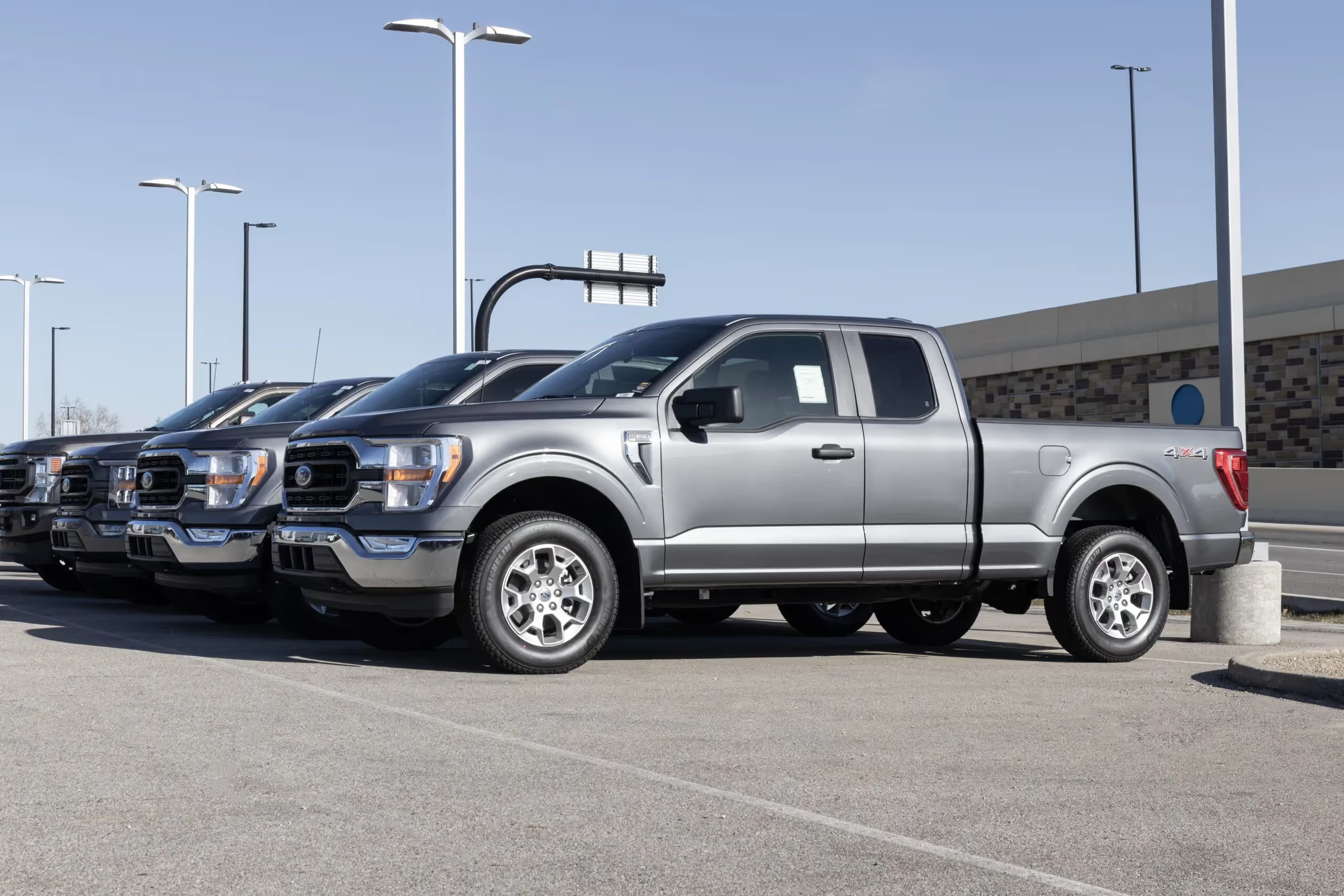
How Should You Approach Rightsizing Your Fleet?
How Should You Approach Rightsizing Your Fleet?
Why analyzing utilization isn’t enough.
In today’s inflationary environment, fleet managers are under increasing pressure to reduce the cost of operating their fleets. Because a fleet’s size is directly proportional to its cost, one of the most effective ways to accomplish this goal is to reduce the inventory of vehicles using a process known as “rightsizing.”
Of course, there are benefits beyond cost savings that come with a rightsizing initiative, including simplification of replacement planning and greater sustainability. Yet, it’s not easy.
Fleet managers are often stuck between leaders looking to eliminate infrequently used vehicles and drivers hoping to retain those vehicles. Navigating this struggle requires a rightsizing process that’s based on facts, non-political, and rational.
Utilization studies: A first step in a rightsizing plan
As a first step toward rightsizing, fleet managers will sometimes perform a utilization study, which analyzes how often each vehicle is being used. In these studies, vehicles are ranked based on their annual mileage and engine hours.
Looking at total utilization may miss the mark. Utilization studies often use the wrong variables and over aggregate the data. Mileage may be the most common utilization metric, but it doesn’ work well. Utility trucks aren’t working when they’re driving on the road. They’re working when they’re parked at a job site. So mileage isn’t a good reflection of how they’re used.
Aggregating information over a month or year doesn’t provide enough information about how the unit is used. A unit that has had one large trip a month could show the same total usage as a unit that takes small trips every day.
We need to shift to looking at usage days – how many of the fleet’s units are being used on each workday. And analyzing utilization alone isn’t enough. You also need to consider maintenance – how many vehicles are in the shop on any given day? This can be measured by looking at open work orders.
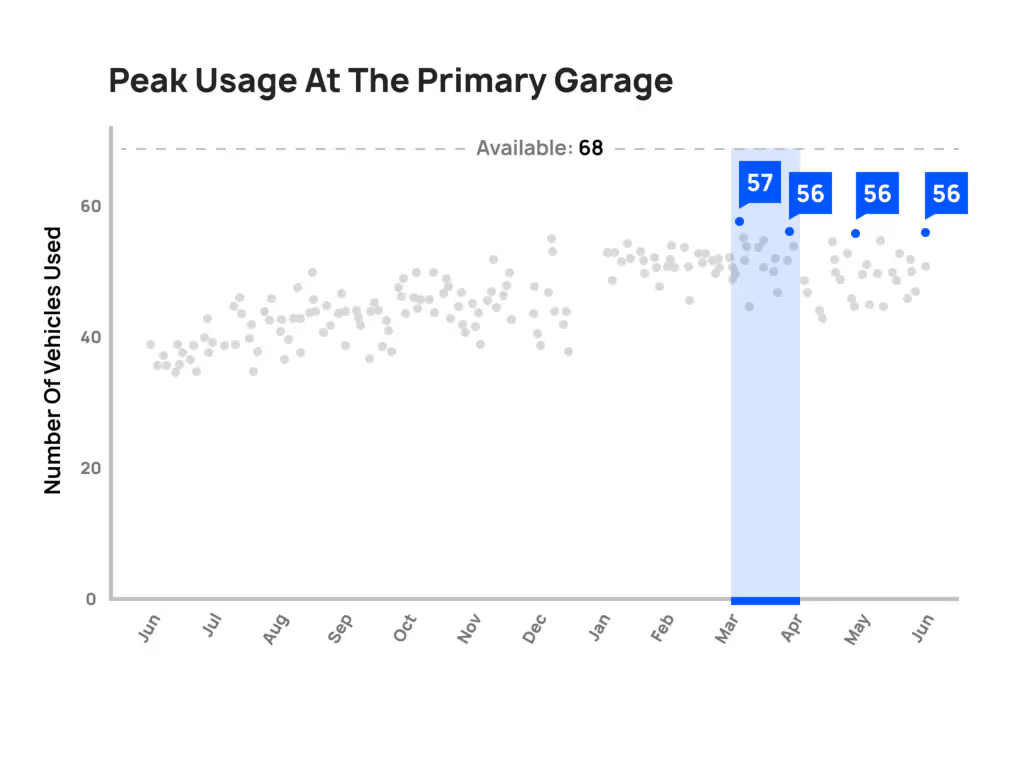
The Utilimarc Rightsizing Formula looks at two things. First, how many vehicles are needed to cover 95% of the days in the busiest month. Second, on average, how many vehicles are down due to maintenance in a day. Add these two numbers and you have your recommended fleet size.
An effective rightsizing model analyzes 12 to 24 months of utilization data by vehicle class and location. It accounts for the impact of seasonality, storm emergencies, mutual aid, and rental vehicles. Using this approach helps shed light on how many vehicles are needed for a typical workday.
At this point, you factor in downtime – the average number of vehicles in the shop – to understand vehicle availability.
One fleet’s approach to rightsizing
Let’s take a closer look at the way one fleet calculated its vehicle need using this process.
Our example fleet started with 68 half-ton pickup trucks available at its primary garage. The utilization study showed that they used 42 vehicles on an average weekday. A used day is set to 5 miles by default but can be adjusted to a higher mileage or an engine hour threshold based on vehicle type.
Most days, there were between 35 and 55 vehicles used.
A deeper look at historic usage levels shows that 57 vehicles would cover 100% of the work needed on any given day. If the fleet had 42 vehicles, it would only cover 50% of the usage days.
Looking at maintenance, there were an average of 1.5 vehicles in the shop each day.
With this data, Utilimarc would recommend a fleet size of 58 vehicles, which would allow the fleet to remove or reposition 10 vehicles. For these vehicles, the fleet would save a combined $540,000 in “capital avoidance,” a term that covers the acquisition cost. The fleet could also save a combined $35,000 in annual operating costs for fuel, maintenance (labor and parts), licensing, tolls, and administrative resources needed to manage the vehicles.
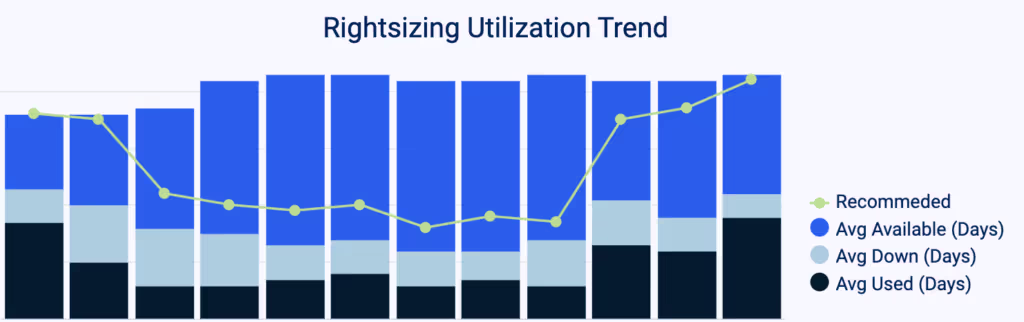
Armed with this data, the fleet was able to apply the same analysis to each vehicle class at the primary garage and then to its seven other fleet facilities. Utilimarc recommended removing 45 total vehicles from these locations including light, medium, and heavy-duty assets.
The resulting overall capital avoidance from the eight locations was $6.2 million – a savings windfall that could be redirected to other areas of the operation. In addition, the annual operating cost for the fleet would shrink by $285,000.
Fleet managers use various strategies when faced with these findings, including redeploying excess units to other locations or specialized assignments. Managing a fleet with a mindset of surplus units can also assist with replacement planning and rental costs.
Looking to reduce costs through rightsizing? We can help.