Fleet idle reporting is more than a buzzword – it’s a critical tool for reducing fleet costs and improving vehicle longevity. Excessive idling is a silent budget killer that does far more than just waste fuel. When vehicles idle, they achieve zero miles per gallon while still putting hours of wear on the engine. This hidden engine run-time leads to higher maintenance needs, shorter vehicle lifespans, and an elevated total cost of ownership (TCO) for the fleet. In this comprehensive guide, we’ll explore how idle reporting and smart metrics help fleet managers and budget-conscious decision-makers cut costs. We’ll back up every claim with recent data from authoritative sources, and show how tracking and reducing idling can translate into fleet maintenance savings and a lower TCO.
The Hidden Costs of Excessive Idling on Fleet Operations
The U.S. Department of Energy notes that reducing idle time not only saves fuel but also “can also reduce engine wear and associated maintenance costs”. In fact, idling is essentially running the engine while parked – burning fuel and shortening engine life without delivering any mileage. Consider the scale of the problem: Argonne National Laboratory estimates that vehicle idling in the United States wastes more than 6 billion gallons of fuel each year, amounting to over $20 billion in lost fuel costs annually. This is fuel that gets burned with zero productive output, draining fleet budgets.
Fuel waste is just the tip of the iceberg. Excessive idling creates wear-and-tear equivalent to driving, even though the odometer doesn’t move. According to The Washington State Department of Ecology, “Two minutes of idling equals 1 mile of driving” in terms of engine wear. This means a truck or car that idles extensively is effectively aging faster than its mileage indicates. Hours of idling contribute to hidden engine hours that will later manifest as maintenance needs or earlier component failures. In the long run, these factors can significantly raise the fleet’s operating costs. As discussed in the next sections, the impacts show up in higher maintenance costs, reduced vehicle lifespan, and a greater total cost of ownership.
Increased Maintenance Costs from Idling
One of the most immediate non-fuel costs of excessive idling is higher maintenance expenses. When an engine runs idle, it isn’t under load, but it still combusts fuel inefficiently – leading to residue buildup and contamination. The Maryland Department of the Environment warns that idling leaves deposits on spark plugs, increases fuel consumption, and reduces the life of exhaust systems. Over time, these effects mean more frequent tune-ups, spark plug replacements, and exhaust system repairs. In diesel engines, long idle periods can cause lower combustion temperatures, which may lead to carbon soot accumulation in EGR valves or diesel particulate filters, further driving up maintenance costs (and potentially causing unplanned downtime for regeneration or cleaning).
Idling also racks up engine hours that count toward maintenance intervals. Many manufacturers specify oil changes and overhauls by engine hour for fleets with high idle time. Argonne researchers note that idling accelerates engine wear and tear, and when maintenance schedules apply to “hours operated” rather than just miles, “the cost of idling is greater than just fuel.” In other words, a truck that idles frequently will hit the equivalent of its service thresholds sooner. This translates into more frequent oil changes, filter replacements, and inspections – all of which inflate maintenance expenses.
The financial impact can be significant. A state idle-reduction campaign in Maryland estimated that “excessive idling can damage your engine and add as much as $2,000 per year in maintenance costs” per vehicle. Those are avoidable costs directly tied to idling habits. Multiply that by dozens or hundreds of vehicles in a fleet, and the maintenance waste becomes substantial. It’s no surprise that industry data show fleet repair and maintenance expenses climbing in recent years. For example, in the trucking sector, average repair and maintenance costs rose about 12% in 2022, reaching $0.196 per mile on average. While many factors drive rising fleet maintenance costs (parts prices, labor rates, etc.), reducing unnecessary engine hours from idling is one clear way to mitigate wear-related upkeep.
Identifying Cost-Saving Opportunities
As you can see pictured, Utilimarc’s Fleet Analytics Solutions provide a clear, intuitive way to distinguish high unproductive idlers and gain visibility into general idling trends across your fleet. The dashboard shown highlights idle performance across multiple vehicle classes and categories, empowering fleet managers to make data-driven decisions with confidence.
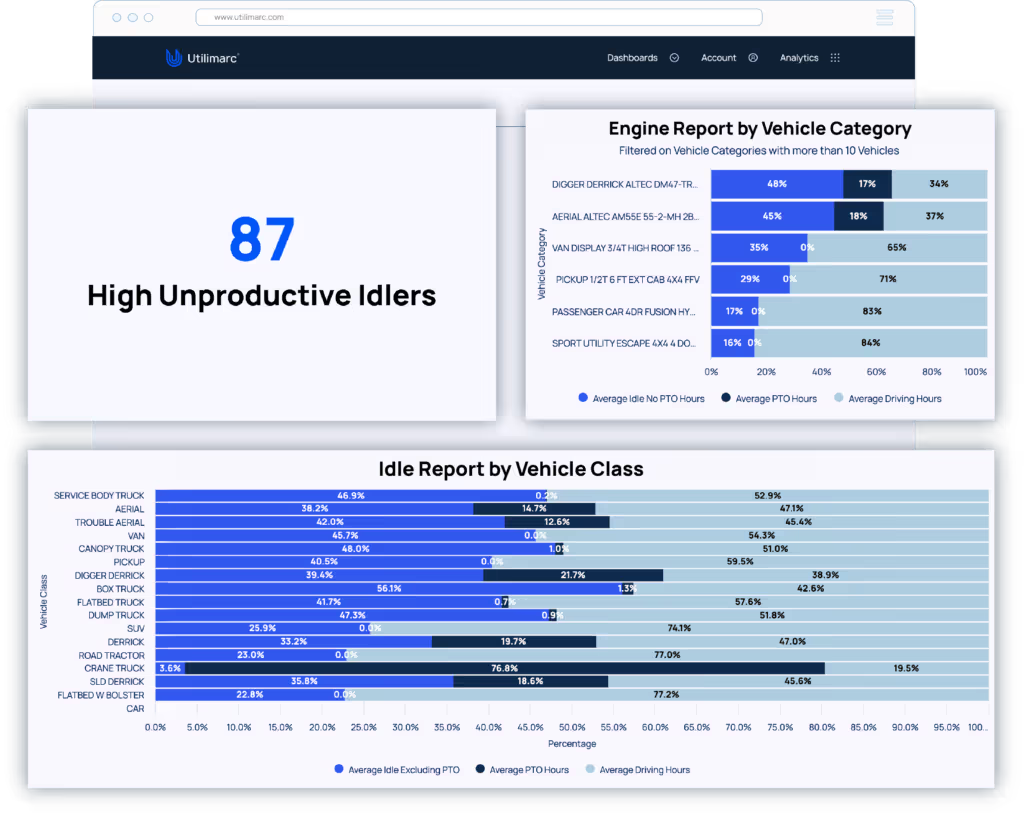
Let’s take a closer look at how an implementation plan and dashboard covering Idle Reporting can directly support your fleet's cost reduction efforts.
Idle Reduction = Cost Reduction
For example, while your pickup truck’s odometer might read 10,000 miles, the engine may feel significantly more worn if it’s also accumulated hundreds of hours of idle time. This wear leads to more frequent oil changes, earlier replacements of emission control parts, and other unplanned maintenance costs that could have been avoided with clearer visibility into idle behavior.
Utilimarc’s analytics capabilities can pinpoint exactly which vehicles and categories are contributing most to idle time, separating idle hours by type—PTO (power take-off), non-PTO, and driving time. This clarity allows fleet managers to quickly identify problem vehicles, compare across categories, and prioritize interventions where they’ll have the greatest impact.
Reduced Vehicle Lifespan and Higher Total Cost of Ownership
Excessive idling can also shorten the overall lifespan of fleet vehicles. Idling often means running the engine at cooler temperatures, which can lead to incomplete combustion and condensation. These conditions contribute to faster degradation of engine oil and internal components. It’s well documented that “idling vehicles… shorten the life of your engine”. Over months and years, vehicles that idle a lot may experience earlier engine failures or need major overhauls sooner than those that do not.
A shorter engine or vehicle lifespan has a direct effect on total cost of ownership (TCO). TCO accounts for all expenses over a vehicle’s life – including purchase price (or depreciation), fuel, maintenance, and resale value. When idling reduces a vehicle’s useful life, the fleet either incurs higher depreciation (more frequent vehicle replacements) or lower resale value due to excessive engine hours. In essence, idling shifts useful life from driving time to non-productive time, undermining the ROI of that asset. If a car or truck was expected to last 10 years or 300,000 miles, heavy idling could mean it needs replacement perhaps a year earlier or with tens of thousands fewer miles because the engine has been effectively “used up” by idling. One university transportation center report concisely states that idle reduction strategies “produce savings in fuel and vehicle maintenance costs and extend vehicle life.”
To illustrate the hidden life reduction, recall the earlier metric: 2 idle minutes = 1 driving mile in wear. Imagine a service van that accumulates 1,200 idle hours in a year (that’s about 3.3 hours per day of various idling). Those 1,200 hours are equivalent to roughly 36,000 miles of engine wear (using the 2 minutes = 1 mile guideline) that won’t show up on the odometer. After a few years of such behavior, the van’s engine might have the wear of, say, 150,000 miles on it while the odometer only reads 100,000. This discrepancy can significantly reduce the vehicle’s residual value when it comes time to sell or require the fleet to retire the vehicle earlier than planned – both of which drive up the TCO.
From a holistic perspective, idling elevates TCO by increasing fuel costs, maintenance costs, and depreciation costs. The Environmental Protection Agency reinforces this, noting that benefits of cutting long-duration idling include “decreasing engine maintenance costs” and “extending engine life”, on top of the obvious fuel savings. Lower fuel and maintenance expenditures, and longer vehicle service life, all positively impact a fleet’s total ownership costs. Thus, as discussed in previous sections, tackling idle time is a key lever for fleet managers to pull in order to control both operational expenses and capital costs over the vehicle lifecycle.
Using Idle Reporting Metrics to Drive Fleet Maintenance Savings
Given the clear link between idling and higher costs, the next challenge is how to identify and curb excessive idling. This is where idle reporting tools and smart fleet metrics come into play. Modern telematics and fleet management systems can monitor engine idle time for each vehicle and driver, providing actionable data. Many fleets now track metrics such as:
- Idle hours and idle fuel consumption per vehicle: Allows managers to pinpoint which trucks or vans are guzzling fuel while parked. For example, a telematics system might report that Truck #12 idled 10 hours last week, burning X gallons of fuel. As noted earlier, just one long-haul truck can easily idle about 1,800 hours per year, using roughly 1,500 gallons of diesel in the process(afdc.energy.gov). Having this data by vehicle highlights the worst offenders.
- Idle time as a percentage of engine running time: This metric shows how much of a vehicle’s operation is spent idling. If a delivery van’s engine runtime is 30% idle (and only 70% moving), that’s a red flag. One pilot program found that by cutting idling from 30% of engine time down to 10%, fleets saved thousands of gallons of fuel and correspondingly reduced wear (raqc.org). Idle reports make such percentages visible.
- Idle events and durations: Many telematics solutions log each idling event (e.g. engine on, vehicle stationary for over 5 minutes) and its duration. This helps identify patterns – perhaps certain drivers leave engines on during lunch breaks or while loading/unloading. Managers can use this insight to coach those drivers (as discussed below) or adjust routes and schedules to minimize unnecessary engine-on time.
- Engine hours vs. mileage: Idle reporting often includes total engine hour readings. Fleet managers can compare engine hours to odometer miles to gauge hidden wear. A high hours-to-miles ratio suggests a lot of idle or low-speed use. For instance, if two trucks both have 50,000 miles, but one has twice the engine hours, its maintenance needs will be higher due to idling. Tracking this can inform preventive maintenance schedules – e.g. performing oil changes based on engine hours for high-idle units, rather than just mileage.
By leveraging these metrics, fleet operators can achieve significant fleet maintenance savings. As discussed above, reducing idle time directly cuts down on engine wear and keeps maintenance needs in check. Idle reports highlight exactly where the opportunities lie. For example, if idle logs show that a handful of vehicles or drivers are responsible for a large share of idling, the fleet manager can focus training or policy changes on those problem areas (rather than a blanket approach). This targeted action can yield quick wins – reduced fuel wastage and less strain on those vehicles’ engines – improving the fleet’s overall cost per mile.
Idle reporting data can feed into predictive maintenance programs. Advanced telematics not only measure idle time but also integrate with maintenance tracking. According to the DOE’s Alternative Fuels Data Center, some fleets use telematics systems that offer features like “consumption monitoring, predictive maintenance, and route planning” to save fuel and optimize operations. For instance, if a truck’s idle hours are accumulating quickly, the system might flag it for an earlier oil change or engine check. By catching wear-related issues early (before a breakdown), fleets avoid costly unplanned repairs. In this way, idle monitoring contributes to a more proactive maintenance strategy, saving money and vehicle downtime.
Idle Reduction Strategies and Improving ROI
Idle reporting is the diagnostic tool – it tells you where the problems are. The next step is implementing idle reduction strategies to actually curb the excessive idling and realize cost savings. Fortunately, fleet managers have a toolkit of solutions, and combining these strategies with data-driven insights can significantly boost return on investment (ROI) for the fleet.
1. Driver Training and Policies: Human behavior is often the root of excessive idling. Training drivers about the impacts of idling and how to avoid it is fundamental. As the AFDC notes, even experienced drivers benefit from training on how fuel economy is “reduced by idling” and other inefficient practices. Fleet managers should establish clear anti-idling policies (for example, “no idling more than 1 minute when parked”) and communicate the reasons – reduced emissions, lower costs, and even compliance with local anti-idling laws. Some organizations create no-idling zones (e.g. at loading docks or school campuses) and post signs as reminders. Education is key: drivers need to know that idling for long periods is not a harmless quirk, but a costly habit that shortens engine life and eats into budgets.
2. Incentives and Gamification: Many fleets have found success by positively incentivizing drivers to reduce idle time. The EPA notes that financial incentives can be effective, and large trucking companies that offer idle-reduction bonuses “have reported success in reducing idling times below national averages”. Incentives could be as simple as a monthly reward for the driver with the lowest idle percentage or a share of the fuel savings achieved. Some fleets use gamification, creating friendly competition among drivers to keep idle times low or improve fuel economy. This not only lowers idling but can improve overall driving efficiency. Tying these programs back to the idle reports (so drivers can see their stats and progress) keeps everyone engaged and accountable.
3. Idle Limiters and Automatic Shut-off: Technology can enforce good behavior. Many modern vehicles, especially trucks, can be equipped with idle limiters – devices or software settings that automatically shut the engine down after a preset idle duration (say 5 minutes) unless overridden for special cases. For instance, police or emergency vehicles might need override options for equipment use, but delivery trucks generally do not. By installing these, a fleet ensures that even if a driver forgets, the truck won’t just keep idling indefinitely. Telematics can also send alerts: if a vehicle is idling beyond policy limits, the manager gets a notification. These tools create an automated check on excessive idling, supplementing driver mindfulness.
4. Idle Reduction Technologies (IRTs): In scenarios like long-haul trucking, some idling is done to power cab comforts (HVAC, electricity) during rest breaks. Here, adopting auxiliary power units (APUs) or other Idle Reduction Technologies can nearly eliminate the need to run the main engine. The U.S. EPA verifies various IRT devices for trucks and school buses. These solutions can reduce idling fuel use by up to 95%, dramatically cutting costs. While there is an upfront investment, the payoff is quick. According to a Department of Energy case, depending on usage and fuel prices, idle reduction equipment can pay for itself in as little as six months. After that, it’s pure savings – the fleet enjoys lower fuel and maintenance bills and longer engine life. This is a clear ROI win, especially for fleets with high idling patterns (e.g. long-haul rigs, utility trucks, or any vehicles that previously had to idle to run PTO equipment or climate control).
5. Route Optimization and Scheduling: Sometimes idling happens due to external factors like traffic congestion or scheduling. Using route optimization software to avoid known heavy-traffic times or redesigning delivery schedules can cut down on idling in traffic. As one strategy guide mentions, fleets can even restrict certain routes during peak hours to reduce time spent in traffic and idling. Likewise, encouraging drivers to shut off engines during longer stops (instead of, say, idling while waiting at a curbside for 10 minutes) can be reinforced through scheduling practices – e.g. instruct dispatchers to give drivers slightly early arrival windows so they don’t feel pressure to keep the engine running at stops. These operational tweaks, informed by idle reports showing where and when idling occurs most, can make a noticeable dent in idle hours.
By deploying these strategies, fleets can significantly lower their operating costs and improve ROI. The return comes from multiple angles: fuel savings, fewer maintenance events, longer vehicle service, and even compliance benefits (avoiding fines in regions with anti-idling regulations). Importantly, idle reporting provides the feedback loop to measure the success of these initiatives. Managers can track reductions in idle hours month over month and translate that into dollars saved. As one EPA report summarizes, cutting idling delivers a cascade of benefits – “decreasing fuel costs, decreasing engine maintenance costs, and extending engine life” – all of which bolster the fleet’s bottom line.
The Takeaway
Excessive idling has long been an overlooked contributor to fleet costs. But the impact on maintenance, engine life, and TCO is very real. Fortunately, today’s fleet managers are not powerless. With the right data, reporting tools, fleet technology, and reduction strategies, fleets can reduce waste and strengthen their bottom line.
Even a few percentage points of idle reduction across a fleet can mean tens of thousands of dollars saved. That’s why idle reporting should be viewed not just as a sustainability initiative, but a core part of operational and financial management.
How to Connect the Dots
Whatever questions you need to answer or problems you need to solve, Utilimarc delivers the right data—and the right technology—to help you do it. Whether you’re using your own systems or need best-in-class telematics and FMIS, we can integrate, provide, and unify your tools into a single, trusted source of truth. Our team helps you get the answers to your most press fleet questions by make your data accessible, actionable, and aligned with your goals.
Contact us to learn about how we can simplify your fleet’s most complex challenges.